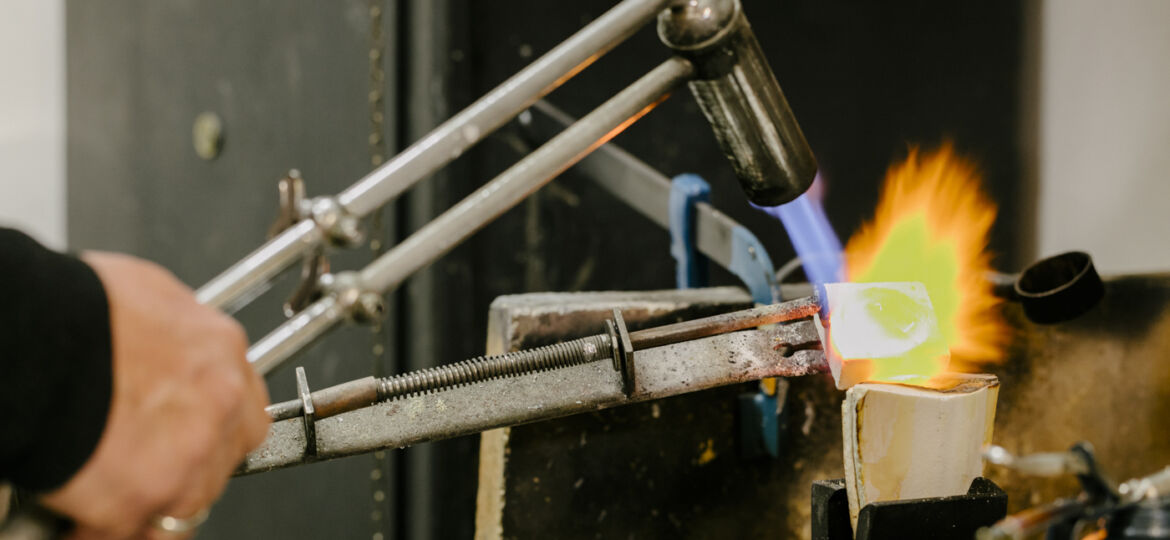
The journey of discovery through the myriad possibilities offered by goldsmithing casting techniques continues. We started from the classic and traditional lost-wax casting to… modern lost-wax investment casting, which involves molding molten metal by forcing it to solidify inside a specially created cavity made of refractory material.
The technique can be used to reproduce many copies of the same object, or to create a unique specimen that cannot be made by hand, such as a face or figure. In this case, the artistic value of the object can be very high: as with a one-piece sculpture, in fact, all the work required to make the wax model is concentrated in a single piece of jewelry.
Cuttlebone casting, on the other hand, is based on the incredible use of the white inner shell of the mollusk.
Although lightweight and brittle,cuttlebone in fact has a tough outer surface and a very tender inner part that is easy to carve. And it can also withstand the high temperatures of molten metal without disintegrating: in short, it has all the characteristics needed to become the casket for a new model and thus for an exciting new goldsmith creation.
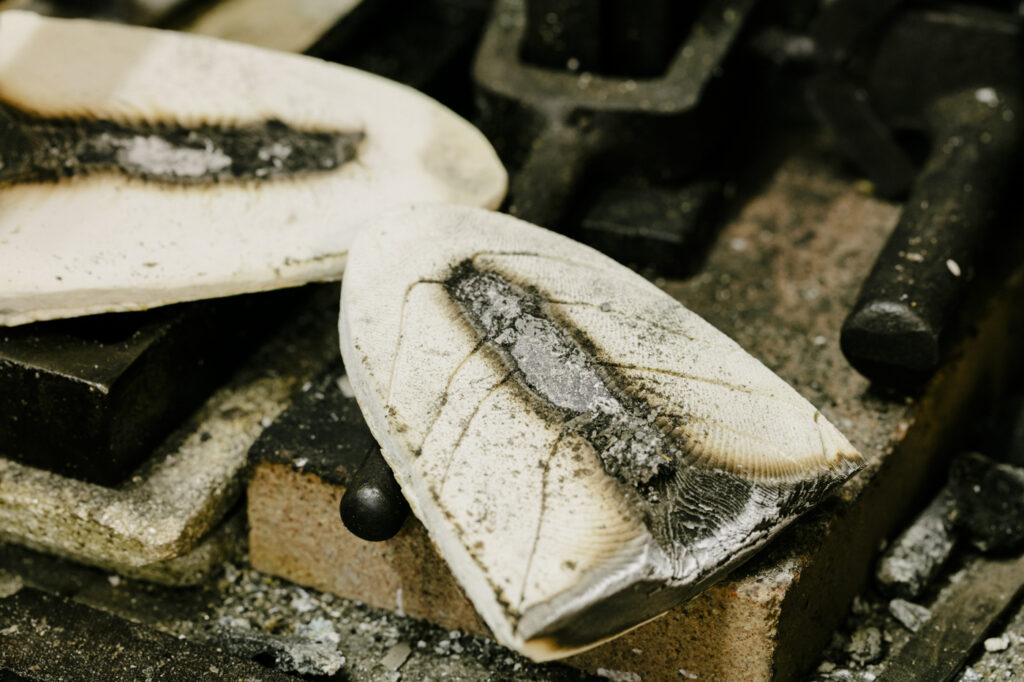
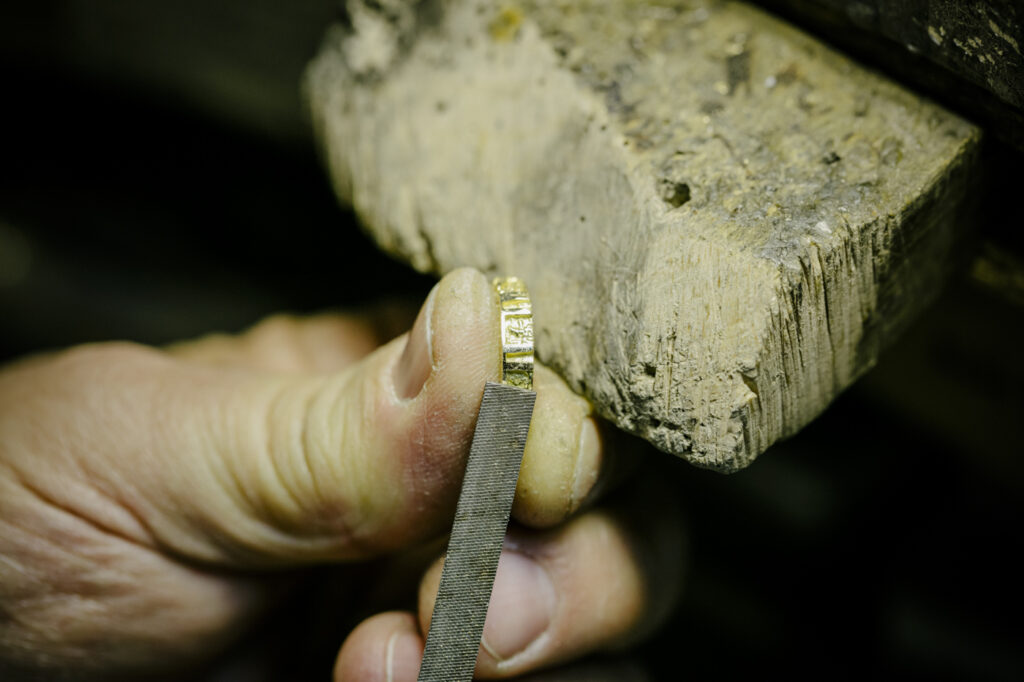
Once the pattern is chosen, the inner tender parts of the cuttlefish bones are smoothed out by rubbing them on emery paper. At this point you compress the model of the object to be reproduced against the two flattened parts. Having made the model, the metal inlet channel is created with a knife, the two parts are reassembled by tying them together with wire, and the molten metal is poured into it.
Here, then, is the world of infinite potential that opens up with fusion techniques, creative and productive processes that make it possible to create unique jewelry, an expression of the original artistic sensibility of thegoldsmith and creative craftsman.